SCDigest Editorial Staff
SCDigest Says: |
The Warehouse Management System or slotting package will have access to those planned pick waves, as well as the inventory records. Therefore, the system can know the demand for a given SKU as far out as a company wishes for the day – and that foresight winds up being the key to making dynamic slotting work.
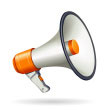
Click Here to See Reader Feedback |
Pick face slotting optimization software has the potential to significantly enhance picking productivity, but for a variety of reasons the category has never reached the level of adoption many expected – though that is starting to change (See Is Slotting Optimization Ready for Prime Time?).
Tony Tyler, president of Ef3 Systems, says the key to really driving productivity through slotting optimization is to make the slotting dynamic, based on expected orders. This was the approach Tyler devised all the way back in 1990 when working on the warehouse system for Canadian Tire’s famous 1.2 million square foot A.J. Billes Distribution Center north of Toronto (named after one of two brothers who founded the retail chain). Nearly 20 years later, it remains one of the most advanced examples of slotting optimization of any distribution operation.
“Slotting choices should be performed dynamically rather than as a batch process,” Tyler says. “To do this, you need to place the picks by product in one or more “look ahead” scheduled cycles or waves, usually to match the transportation schedule and transit times.”
The idea works like this: pick waves are pre-built to service the day’s demand and considering factors such as carrier schedules, store delivery appointments (for retailers) and other requirements and constraints.
In Canadian Tire’s case, the waves were designed to be short – as little as just 20 minutes each – and the operation was supported by a large amount of automation. But the concept can work in many other less automated scenarios.
The Warehouse Management System or slotting package will have access to those planned pick waves, as well as the inventory records. Therefore, the system can know the demand for a given SKU as far out as a company wishes for the day – and that foresight winds up being the key to making dynamic slotting work.
Another critical element to the Tyler/Canadian Tire approach is that pick locations, such as traditional case pick from pallet rack, are always picked to zero. With that design in mind, a new pick position for each SKU that the system knows will go to zero is created and filled 1-2 waves before the wave that the system knows will require more picks of that SKU. The specific placement of the new dynamically created slot will depend on the level of demand (to reduce picker travel time), the SKU’s weight (heavier items before light ones) and other factors.
“Do not place a replenishment in the same slot but determine how long (number of waves) it has taken to empty the pallet or case rack and then adjust the position within a prioritized and commoditized slot list for that product according to its priority and handling characteristics,” Tyler added. “Select an empty slot according to the latest determined position in the list and direct the replenishment to that slot one cycle ahead of when it will be needed.”
(Distribution and Materials Handling Article - Continued Below)
|