From SCDigest's OnTarget e-Magazine
- Nov. 15, 2012 -
RFID and Auto ID News: Can RFID-Based System Deliver More Productivity for Very Narrow Aisle Forktruck Movements?
Software Controls will Manage the Movements Horizontally and Vertically; Up to 25% Efficiency Gains, Jungheinrich Says
SCDigest Editorial Staff
Can productivity in very narrow aisle forktruck systems be improved by as much as 25% through use of RFID location systems and smart truck controls?
SCDigest Says: |
 |
Holste adds: "The real question is why in the end an operator is needed at all. Automating that final step of grabbing or putting away the pallet is not that much of a challenge."
|
|
What Do You Say?
|
|
|
|
Maybe yes, according to Mitsubishi Caterpillar Forklift America Inc. (MCFA), which announced this week the availability in the North American market a system developed in Europe by Jungheinrich that uses this innovative approach. MCFA is a distributor of Jungheinrich products in North America.
According to a press release, the systems uses RFID identifiers on the aisle floor that connect to a reader on the truck, part of the overall Warehouse Navigator system from Jungheinrich.
The basic idea is this: humans, with all their frailties, are usually cautious when moving a VNA truck down the aisle and moving the forks into position to put a pallet away or pick-up a load for a customer order or replenishment.
But the Warehouse Navigator System can make the move down the aisle and raise the forks to the location automatically. It does this by using the RFID tags in the aisle to measure the X-coordinate of the destination, and an internal system to precisely and dynamically measure the vertical height of the fork lift.
The system can be integrated directly with a Warehouse Management System to receive the location for pallet putaway or pick-up automatically, at which time the VNA truck moves, shall we say, with "confidence" to both get to the location position down the aisle and raise the forks to the correct height.
Jungheinrich says its software optimizes the speed and relation between the horizontal and vertical movements to produce the minimum possible total travel time.
In other words, the fork truck operator is simply along for the ride, uninvolved in moving the VNA truck down the aisle or raising and lowering the forks to get to the location. The operator of course does take responsibility to move the forks to pick up or putaway the pallet.
One key is optimally first lowering the fork for rapid horizontal travel, and then smoothly raising the forks back up in a parabolic type motion that produces the best total result (see graphic below). Again, there is no need for the operator to do this manually, clearly a travel time productivity enhancer.
Jungheinrich Says Productivity Gains Come in Part
from Perfect, Parabolic Move of Forks Up and Down
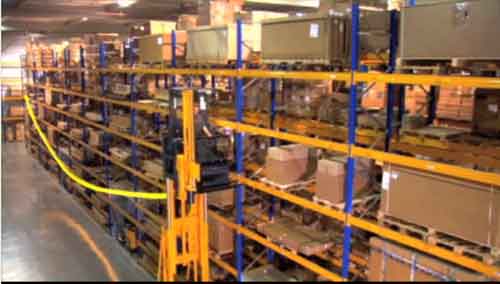
Additionally, the operator does not need to scan a bar code or otherwise verify the action. The Warehouse Navigator system sends that notification on to the WMS based on the location and the action of the forks.
All told, this can lead to productivity gains of as much as 25%, Jungheinrich says. The system can also be used for "order picker" trucks for case picking, with similar potential benefits.
(RFID and AIDC Story Continued Below)
|