Below are a number of steps I have found useful for better managing slow movers:
Get Your Arms Around the Data: The first place to start is to get a sold handle on the data. Just what is the profile of the SKU velocity in your DC?
I have often found that companies do not have that data readily accessible, and are often surprised by what such an analysis reveals.
Below is an example analysis I performed for one client several years ago. The chart shows that 70% of active SKUs fall into the slow mover classification - amounting to less than 15% of the volume. While this represents a fairly normal profile, depending on the total number of SKUs involved, even this level can present issues that can slow down the performance of your supply chain and increase your cost of operations.

Regularly building and analyzing a velocity profile such as this is essential to create a baseline for considering slow SKU mitigation strategies.
Communicate the Facts to Marketing and Others
In my experience, marketing and finance often simply do not know, or do not pay much attention to, the level on inactivity in these slow moving SKUs. Often, SKUs will have zero sales for a given analysis period.
Communicating the velocity data on a regular basis can serve as a catalyst for these othe functions to look at the problem more closely – and maybe eliminate some portion of those slow movers altogether.
They may ignore the data, and even if they take some action it won’t eliminate all your problems with slow movers, but it may result over time in the DC getting some relief.
Rethink Slotting
One obvious use of the profiling data is to rethink your current slotting decisions. Most companies that do not have an automated slotting optimization program find that they often have some slow movers slotted in premium pick areas. They may also be putting away slow movers in storage zones geared for higher velocity SKUs.
Seasonality can play a big role here. A seasonal SKU can see lots of volume for awhile, but then dramatically drop off out of season – yet, it remains in a high moving storage and/or picking zone.
While automated slotting software is great to manage this analysis and make recommend changes to slotting, excel/access type analysis can often lead to better slotting decisions that can improve DC flow and productivity by placing slow movers where they should be stored.
Rethink Storage Modes
A “one size fits all approach” to storage often adds to the issues caused by slow movers.
totes Isotoner, for example, initially stored all the SKUs required for its substantial piece pick operations in carton flow rack. Later, it decided to switch many slower movers to static shelving, increasing the density of storage for those SKUs and to expand the facings for many of the fastest movers, reducing replenishment efforts.
If you have the right WMS support, you might also consider greater use of mixed SKU storage locations for slow movers. Half-pallet positions are another option many companies utilize, which also frees up space.
I have also frequently implemented a creative solution for slow movers in full case “pick to belt” applications.” While pick-to-belt modules can be very efficient for picking, they are not all that great when it comes to space utilization.
The sketch below shows a typical two level high double-deep pallet flow pick module. The vertical clearance for the second level mezzanine is shown at 7.5 feet above the floor, which is about the minimum requirement for such applications. Unfortunately, this arrangement can leave a large void above the top of the pallet loads.
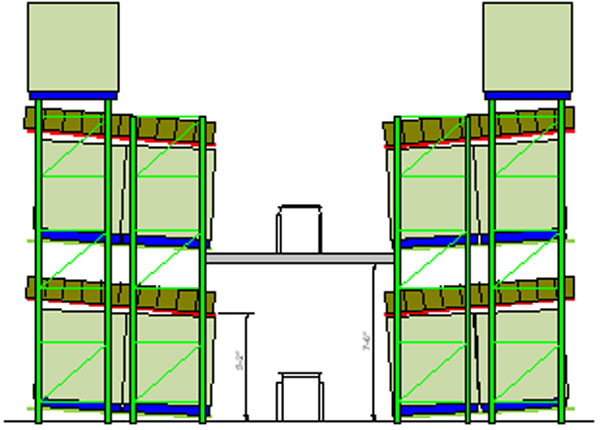
Often, this dead space can be put to good use by installing a shelf of carton flow lanes into the pallet flow rack. This can be easily accomplished by utilizing standard components readily available from rack suppliers. Now, this previously dead space becomes a productive storage and on-line picking location for slotting your slow movers, while freeing up off-line static shelving and bin storage space for other uses.
Consider Dynamic Slotting
Many companies maintain a fixed picking position even for slow movers, taking up valuable space that is poorly utilized.
Your WMS may support dynamic slotting, or if not your IT department may be able to develop this capability summary, when an order is released that includes a slow moving SKU without a dedicated pick face, a temporary pick slot is created by the WMS, and that slot filled with product from reserve storage to meet that need (alternatively, some companies may even pick slow movers direct from reserve).
Automation Can Play a Role
While it obviously may require significant investment, some companies find that use of automating slow moving SKU management can pay off.
For example, I have seen several companies place slow moving inventory into an automated storage system that creates high density/efficient product storage without a dedicated pick face for each slow moving SKU. When a pick of one of those SKUs is required, the storage system “serves up” the SKU to a pick face. When order fulfillment is complete, the automated storage system places that SKU back into high density storage.
This is simply an automated form of the dynamic slotting approach described above.
Some companies may also choose to use carousels to handle slow movers. It is noteworthy that carousels are used extensively in service parts distribution – an environment often characterized by huge numbers of mostly slow moving SKUs.
Coty Inc., the world’s largest fragrance company, found that while its 900 slowest moving SKUs amounted to only about 2 percent of total volume, they led to substantial bottlenecks in order processing.
Coty implemented two 65 foot long, five-shelf, light-directed horizontal carousels, which led to much more effective picking operations and storage density for those slow movers.
|