|
|
|
|
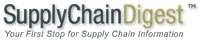 |
|
|
|
|
|
Manufacturing Focus: Our Weekly Feature Article on Topics Related to Manufacturing Management |
|
|
|
|
|
|
 |
|
|
More Interest than Ever, says One Quality Consultant, but Little Real Progress; Top 10 Reasons Root Cause Programs Flounder
|
|
|
SCDigest Editorial Staff
SCDigest Says: |
The interest in understanding and teaching root cause analysis is at an all-time high, according to one quality industry expert – but still badly implemented at far too many companies.
Click Here to See Reader Feedback
|
“Root Cause Analysis” is one of the foundations of most versions of quality improvement, Six Sigma and even Lean initiatives designed to drive continuous improvement and identify waste in time or materials. The basic idea: ruthlessly search to identify and fix the true source of any given supply chain or manufacturing problem, as opposed to efforts to simply address the immediate symptoms.
The interest in understanding and teaching root cause analysis is at an all-time high, according to one quality industry expert – but still badly implemented at far too many companies.
According to Mike Micklewright, president of QualityQuest Inc., a Chicago-based consulting company, despite the widespread interest in root cause techniques, root cause analysis processes at most companies “suck,’ and it’s time more companies figure just why that is.
We found Micklewright’s ten somewhat irreverent reasons for many root cause analysis process failures, as recent published in Quality Digest, to be both entertaining and enlightening:
- It’s More Fun to Blame the People: Too many root cause efforts focus on finding a human culprit, rather than really looking at the process. “The situation is also easy to rectify, because all one has to do is to counsel, retrain, talk to, and convince them that they need to pay more attention, or better yet, fire their butt,” says Micklewright, rather than the hard work of fixing the system.
- Top Managers Don’t Want To Find Out They Are To Blame: Quality guru Dr. Edwards Deming said 90 percent of root causes are due to common cause variation, and that only top management can control this type of variation. “It’s easier to send only manufacturing personnel to training and make them feel they are root causes and ensure that they fear making another mistake,” Micklewright says.
- I Was Told to Shut-Up after Asking “Why?” One Time: Too many companies don’t want to really, really get at the root cause of problems stemming from overall design or poor processes.
- We Don’t Have Time to Think Long-Term Right Now: Wall Street and other pressures never leave enough time or resources to address root cause problems. Companies pretend they will get to root-cause analysis next month, or next year, and then really resolve the problems. They never do.
(Manufacturing Article - Continued Below) |
|
|
|
CATEGORY SPONSOR: SOFTEON |
|
|
|
|
|
|
|
5. Fixing Root Causes is too Expensive: By not really asking the right questions, the root cause issue and its solution often gravitate towards answers that require a lot of expense to implement. That is often simply incorrect – solutions can be simple, inexpensive, and should always save money. “This is not the perception of the majority of leaders,” who tend to think in terms of “big” solutions, says Micklewright.
6. “My People can’t do this, and I’m a Micromanager”: Too many managers think they are the only ones smart enough to figure it out, and they don’t have the bandwidth to tackle much of anything. These managers would also rather give their people the fish than teach them how to fish.
7. It Requires Thinking: Too much day-to-day pressure to actually apply all that black belt knowledge.
8. Why Do Root-Cause Analysis Training? We Can Buy the Solutions Anyway!: It’s much easier to buy 5S (sort, straighten, shine, standardize, and sustain), value-stream mapping, kaizen, TPM (total productive maintenance), quick changeover, all of the Six Sigma tools, and an ISO 9001 certificate than to go through the hassle of determining root causes,” says Micklewright. If a company wishes to copy Toyota, they should copy how Toyota did root-cause analysis, not 5S, he adds.
9. We Don’t Practice It at Home. Why Should We Do It at Work?: “We rarely get to root causes at home, in our neighborhood, or in our country. We aren’t accustomed to it,” Micklewright says. “So we go for the quick fix, the new drug. This gets carried over to work and we continue to buy the latest drug at work—ISO 9001, Six Sigma, lean tools, and products from India and China.”
10. Getting to Root Causes would Require us to Work with other Kingdoms: Most problems are cross functional. To fundamentally address these kinds of issues “would require true process orientation or value-stream management. Most companies don’t have this; they talk of this only during an audit, a kaizen event, or a Six Sigma project.”
The bottom line from Micklewright: “It’s best to discover the root causes of why root-cause analysis sucks at your company before conducting more training!”
Do you share a pessimistic view on the real success of “Root Cause Analysis” techniques? What is your reaction to Micklewright’s list of reasons for poor root cause processes? What would you add? Let us know your thoughts at the feedback button below.
|
|
|
|
|
 |
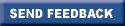 |
 |
|
|
|
|
|
|