Just back from Chicago and CSCMP 2009, and as always, below is my review and comment on this year’s event. Thousands of you have already watched our daily video reviews this week, which you can also find here: CSCMP 2009 Day 1, Day 2, and Day 3 video reviews.
The crowd was down this year, at about 2500 versus the 3000 or so that CSCMP has had the last couple of years. But every event is having attendance problems and, all things considered, this year’s number is pretty good. I heard several stories of companies that used to send more people, but this year approved a much smaller contingent. That means the total number of companies coming was probably closer to the recent norm than the actual attendance numbers.
In 2008, it was hard to focus on the supply chain while the financial system was crashing all around us (Bear Sterns collapsed that very week, as the stock market cratered). Nothing like that this year of course and, in general, the overall economic mood was cautiously optimistic.
Gilmore Says: |
Kraft is now highlighting the transportation savings it can jointly achieve with customers, and its impressive technology, to drive additional volumes with its retail channels.
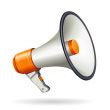
Click Here to See
Reader Feedback
|
For the first time in a while, sessions were 90-minutes long this year, versus the 60 minutes of the past few years. I suspect the drivers of that change were some feedback about the conference having too many sessions lately, and expectations that attendance numbers would be down. However, I would encourage a return to shorter sessions (and fewer “tracks”), first, so that you can get in one more session each day, and second, because the sessions that took the whole 90 minutes really started to drag in the last third, from what I experienced.
Before reviewing key sessions, a quick “shout out” to all companies that gave presentations this year, but especially to Coca-Cola, Kraft, and Intel, each of which spoke at a minimum of three sessions. These industry events just don’t work without that type of practitioner contribution – we all owe them our gratitude. On the other side, The Limited Brands, which has been perhaps the most consistent public contributor of SCM insight (thank you) over the last 10 years or more at these types of events, was absent this year, unless my review of the program guide was faulty. Hope to see them again soon.
For the first time in awhile, the Day 1 key note speaker was a true supply chain professional, that being Gary Maxwell, Sr. VP of International Supply Chain for Wal-Mart. The key message – you don’t need to be and, in fact, often shouldn’t be “world class” in different markets around the globe. You instead need to be “best in market,” scaling the supply chain and automation to each market’s needs, culture, labor and land costs, etc. He implied that some Wal-Mart competitors were, in fact, investing too much in automation and developed economy supply chain practices in many markets. In my view, this “micro-logistics” concept will be a key theme for the next decade.
I loved the presentation by Jim Kellso of Intel on how it utterly re-invented its supply chain for a new, much lower cost chip (the “Atom”). A supply chain cost of $5.50 works for a chip with an ASP of $100, but not with one that is priced at $20.00 heading towards $10.00. The early insight – incremental improvement of the existing supply chain would not get SCM costs (largely inventory) down to the needed level of $1.00 or so per chip. Intel had to start from scratch, throw out all of its pre-conceived notions, and focus solely on hitting that cost target.
The result: a change from a largely make-to-stock approach with an 8-9 week cycle time to a make-to-order model with a two-week cycle time and fixed orders (versus the multiple order changes that occurred in the existing model). Inventories are down dramatically, and the need for distribution processes substantially reduced. While the opportunity was there all the time, it was the new cost imperative that drove the change.
John Wooten of Clorox gave an interesting presentation on how it now rigorously compares actual lane-carrier costs versus what the results should be based on carrier bid optimization processes and resulting contracts. While there will inevitably be some “leakage,” for a variety of reasons, for many companies that can be as high as 10% or even more. By using a transportation “Business Intelligence” system to compare actual versus expected, Clorox has reduced its leakage to just 1-3% each quarter, saving millions.
While on the topic of transportation, Michael Cole and Kelly Rae of Kraft Foods gave a presentation on the company’s adoption of new TMS and yard management system (YMS) technologies that, at one level, was nothing that new, but from another perspective, really was. First, it highlights how much more advanced today’s Transportation Management Systems are versus those that are even 5-7 years old. Second, Kraft just may be the most aggressive and successful practitioner of “continuous moves,” which, in fact, has been something of an urban legend in transportation circles.
Kraft is now highlighting the transportation savings it can jointly achieve with customers, and its impressive technology, to drive additional volumes with its retail channels. I loved its focus (and resources) on “Collaborative Transportation Engineering.”
I am pleased to say my own presentation on “Integrated SCM Planning and Execution” had a literally full house of some 150 attendees. Key message: integrated planning and execution is now becoming critical and a “next big thing,” and in the next 3-5 years, operational and some tactical planning will start to blur with execution processes as we move to “sense and respond” networks. See the SCDigest web site to download the Chief Supply Chain Officer Insights report.
Tan Miller, now at Ryder University, but until just recently at Pfizer and then Johnson & Johnson via acquisition, gave an interesting presentation on how he led development of a logistics Decision Support System (DSS) that I must say sounded quite impressive – and, in fact, is something I have proposed for years. It is part advanced planning system, part unique approach to providing decision support few logistics managers have. Quick example: the DSS modeled receiving, storage and shipping capacities at each DC, and regularly compared those capacities with future forecasts to highlight potential DC issues well before they occurred.
There was so much more at the conference, but that’s all I have room for here. More detail is available on the daily summary videos, and we will be publishing individual articles on many of the sessions in SCDigest On-Target in the coming weeks.
As always, I am compelled to offer one suggestion for CSCMP and CEO Rick Blasgen, and that is to make the process for selection of track chairs and individual presentations more clear and transparent. I heard a number of complaints about this in the weeks leading up to and at the conference, and I think those complaints have merit. We call for transparency and process consistency in our supply chains, and we should, therefore, expect the same in the industry’s premier conference. How this really works frankly is something of a black hole. Let’s make it more open and consistent.
But I had a great time in Chicago, and the quality of the presentations I went to was quite high. As always, I will be in San Diego for CSCMP 2010, and hope to see you there.
Did you attend CSCMP 2009? Why or why not? If yes, what were your thoughts on this year’s conference? What sessions did you find most valuable? Let us know your thoughts at the Feedback button below. |