It's back.
In 2006, we put together our list of the greatest supply chain disasters of all time, a column and report that proved to be very popular. I have even been asked to give speeches on our list a number of times.
The good news is that really major supply chain disruptions happen rarely enough that there is no need or benefit from updating the list too often. It was also interesting that in 2006, the most recent incidents on our list were from 2001.
Well, we've had a couple of pretty "good" supply chain snafus since then, making it time to update the list. Hope you enjoy.
Gilmore Says: |
Note most recent disasters are not technology related, as many earlier ones were. They are all process failures. Interesting.
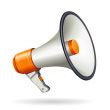
Click Here to See
Reader Feedback |
The list is totally subjective, although, then and now, a lot of work and research by me and the staff went into it. Just to be clear, the list is meant mostly to be for fun and maybe shed a few lessons for us all, not to "embarrass" any given company receiving the "honor."
Most of us have experienced major issues of one kind or another. Fortunately, most often they don't make the press, or if they do, it's on the back pages. Just a few lucky ones get to grace page 1 of the Wall Street Journal.
As I have often said, the good news is that suppy chain management is commonly called out by CEOs these days as key drivers of corporate strategies and success. But with that comes added pressure - when the supply chain fouls up, it is going to get the public blame as well.
So, what did we add for this year? Four disruptions/problems that have happened over the past 3 years, and one old one that we just missed the first time around.
The new ones are the Boeing Dreamliner 787 outsourcing snafu, the Mattel China toy recall disaster, Loblaws logistics network redesign foibles, and (I am sure most controversially), Wal-Mart's struggles getting its RFID program off the ground.
The "oldy but goody" that we added is the strange saga of the Big Three automakers trying to launch the Covisint e-commerce exchange - quite unsuccessfully.
I hope all of you are familiar with the excellent work of Dr. Kevin Hendricks of The University of Western Ontario and Georgia Tech's Dr. Vinod Singhal on the impact on shareholder value from supply chain disruptions. It had a significant impact on awakening companies to how damaging such even modest disruptions can be, and was a key catalyst for the focus on supply chain risk management so many companies have today. Dr. Signhal graciously made that report available through SCDigest, which can be found here: SCM Disruptions and Shareholder Value.
So, our summary list is presented below, in order from worst to not quite as worse. A much more detailed version can be found in our new report on the topic, downloadable by clicking here. It's a fun read.
- Foxmeyer’s "Lights Out" Warehouse: New order management and warehouse automation systems lead to inability to ship product and failure to achieve expected savings; bankruptcy and sale of the multi-billion drug wholesaler follow in mid-1990s.
- Boeing Outsources its Way to Delays and Big Hits to Bottom Line: Plans to radically overhaul the supply chain for the new Dreamliner 787 aircraft sound good, but massive problems with component deliveries in 2007 leads to two-year delay in aircraft launch and some $2 billion in charges to fix supplier problems. Ouch.
- GM’s Robot Mania: CEO Robert Smith spends $40 billion in the 1980s on robots that mostly don’t work, while Toyota focuses on “lean” and cleans up.
- WebVan Automates its Way to Oblivion: $25 million automated warehouses just make no sense given the market; company goes from billions in market gap to gone in just months in 2001.
- adidas 1996 Warehouse Meltdown: Not a well known story, adidas can’t get a first and then a second warehouse system and related DC automation to work. Inability to ship leads to market share losses that persist for a long time.
- Denver Airport Can't Manage the Luggage: New airport opens late in 1995 due to failure of highly automated, hugely expensive system, which never really works and is completely shuttered eventually.
- Mattel's China Syndrone: Mattel's highly publicized recalls of tens of millions of toys made in China in 2007 due to safety issues such as lead paint became the poster child for anti-offshoring interests. Hit to the bottom line and brand are huge, and drop in stock price is permanent.
- Toys R Us.com Christmas 1999: On-line retail division can’t make Christmas delivery commitments to thousands; infamous “We’re sorry” emails on Dec. 23; eventually, Amazon takes over fulfillment.
- Hershey’s Halloween Nightmare 1999: New order management and shipping systems don’t start right, as Hershey can’t fulfill critical Halloween orders; $150 million in revenue lost as stock drops 30%.
- Cisco’s 2001 Inventory Disaster: Lack of demand and inventory visibility as market slows leads to $2.2 billion inventory write-off and stock price cut in half.
- Nike’s 2001 Planning System Perplexity: New planning system causes inventory and order woes, blamed for $100 revenue miss as stock loses 20%.
- Wal-Mart's RFID Saga: The end result may have been to move the RFID industry along from a technology perspective and spur overall interest, but the six-year Wal-Mart RFID drama required significant investment in time and dollars for Wal-Mart and many of its suppliers that can't possibly have delivered a payback. The program still seems confused, and Wal-Mart clearly forgot the axiom about avoiding over-promising and under-delivering.
- Aris Isotoner’s Sourcing Calamity in 1994: Then a division of Sara Lee, Isotoner decides to shut successful Manila glove/slipper plant to chase even lower costs elsewhere; costs rise, quality plummets, revenue cut by 50%; soon sold to totes Inc.
- Auto OEMs Get Trading Exchange Fever: Ford, GM and Chrysler announce wild plans and $250 million in investment for giant online e-commerce exchange called Covisint in early 2000. Publicly say that they expect to IPO it in two years for market cap of $20-30 billion. Internet stock bubble starts to burst just weeks later, costs are wildly out of control, technology strategy is all over the map, numerous CEOs, and soon an almost total disconnect between Covisint and the original concept. Total loss for the OEMs, and Covisint eventually sold off, though operating successfully today with a totally different mission.
- Loblaws Redesigns itself into Supply Chain Problems: I am sure it was a good idea, but Canadian grocer Loblaws' plans for a significant logistics network makeover ran into poor execution problems in the second half of 2005. Company blames two rotten quarters on high costs and lost sales from the effort, CEO apologizes to shareholders, and though the issues largely stabilize by early 2006, the stock price has never recovered from the hit.
- Apple Misses Power Mac Demand: In 1995, Apple plays conservative with commitments and capacity and can’t deliver on demand for new PCs. Market share takes permanent hit.
Quick notes. We obviously may have missed some. If you have any candidates, please share at Feedback button below. Someone last year told me a story of a foreign auto manufacturer that had to destroy a literal "boat full" of cars that were shipped here for a reason I can't remember. Please send that story if you have it. Also, note most recent disasters are not technology related, as many earlier ones were. They are all process failures.
Interesting.
What do you think of our list of top supply chain disasters? Any lessons learned? What would you add or delete from the list? Let us know your thoughts at the Feedback button below. |