I've already milked the new year thing pretty well, with a couple of summaries of 2014 and then a couple of columns on supply chain predictions from various pundits and analysts. While it is admittedly a bit late for new year's supply chain resolutions, believe it or not I have never done this before, so I am going to give it a go even at this modestly late date.
I hope I am avoiding the obvious here, and just like with good personal new year's resolutions I focused on things that most of us know we need to do in our supply chains, but have a hard to mustering the will and the discipline to get them done. So here we go:
Map your Extended Supply Chain: Our collective supply chain eyes were opened in 2011 as a result of the earthquake/tsunami in Japan, and then severe flooding in Thailand that decimated key suppliers in the high-tech sector.
Gilmore Says: |
I think even many consumer goods companies aren't quite sure what demand-driven really means or what it takes to get there - and becoming demand-driven certainly applies to many more than companies in just that sector.
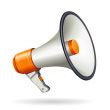
Click Here to See
Reader Feedback
|
Both events exposed risk, often further back in the supply chain, that companies did not realize existed - for example a dual sourcing strategy made irrelevant when both suppliers were in the same heavily damaged regions of Japan or Thailand.
The head of procurement for Toyota and its vaunted supply chain said: "Our assumption that we had a total grip on our supply chain proved to be an illusion," in one of the great supply chain quotes of all-time.
The result: a multi-year Toyota effort to map its full extended supply chain, down to the tier 3 and 4 level. Such a project can be a huge effort, but once complete is much easier to maintain than compile initially. Such an effort will not only expose unknown risks but lead to better overall understanding of your supply chain and - if done right - can be used for other insights, such as demand sensing, as contract manufacturer Flextronics does with its upstream, indirect suppliers. It may be time for you to start such a project tis year.
Model Your Supply Chain: A relatively small but growing number of companies maintain an active network model of their supply chains that they use for on-going decision-making, from inbound supply flows to what products to make where. I saw a presentation from Target last summer, and it is regularly analyzes six or so logistics areas using such a model on a near continuous basis.
I firmly believe companies doing this have a significant competitive advantage over those which do not, and that the ROI from a small team of full-time network analysts - maybe even just a single person - is very high. Yet most won't still yet make the investment.
In a complex dynamic world, with oil prices falling by 50% in a matter of months, the US dollar rapidly gaining strength, lots of complexity and more, a model of how your supply chain works that can be used to answer questions and make optimal decisions is no longer a luxury. I recommend you start building your model in 2015.
Develop a Talent Strategy: Do you really have a plan for finding and developing supply chain talent? A few leaders do - but not many. A few years ago, Pepsico took a look at this - and wasn't happy with what it found. Succession planning was poor, usually just at the very top levels, and it turned out often the same person was slotted as the successor for a whole bunch of positions. There was no real development plan to get current managers the additional skills they needed to move up the ladder.
Pepsico fixed all that over a couple of years, and now has a true talent management strategy and program. I also like Texas Instruments' global database of supply chain talent, which led to the realization that often when in the past they might have looked outside the company to fill a role, maybe the person they needed was already in TI, maybe working in Singapore.
There are very few companies that put in the effort to really get supply chain talent management right. Make 2015 the year you start the journey.
Start Benchmarking: In general, we do far too little benchmarking in the supply chain. I am referring not just to maybe participating in some survey or service that allows you to compare your results (sort of) with those of others, but meeting with companies to see how they do things, and swap and compare ideas and practices.
Ok, if you're Kroger then Publix is unlikely to welcome you in with open benchmarking arms, but you would be surprised how open most companies will be to the idea. And there can be great value in seeing how companies in almost any sector do certain things. For example, how a chemicals company does sales & operations planning might certainly provide some insight to a consumer goods company. It used to be the firms from all sorts of sectors trouped up to Maine to see how LL Bean handled individual piece picking in its DC. Maybe they still do.
So pick up the phone and set up a visit time with some company say 50 miles or less from your place of business. For most, there will be many such opportunities. If you have to go a little further, it will still be worth the effort. You should resolve to do this at least twice a year - and offer to reciprocate the service for others as well. After a few years of doing this important but not urgent task, I almost guarantee you will have learned some valuable insights and ideas. The only real barrier is inertia.
Review Your Technology Portfolio: Do you know exactly what software you have where? Do you have any "shelfware," meaning software you paid for but never implemented, either in total or at certain locations? Do you have options in your contracts with existing vendors for additional products that you have never exercised?
All these are issues for many companies, especially global ones, who often have all kinds of different software and contracts across the world.
Let 2015 be the year you get on top of all of this - do a complete supply chain technology portfolio assessment. You may just find you own some things you didn't realize. It may be possible to convert an option for a traditional solution into a newer-Cloud-based version. And on a related note, it's almost always a good idea to have existing software vendors send in an expert to see how you could get more out of what you have now. Smart companies do this regularly - but most unfortunately do not.
Paint a Vision for becoming Demand-Driven: In the early 2000s Procter & Gamble came up with the "consumer-driven supply chain" concept, which the then AMR Research morphed into its demand-driven supply networks. Rightly or wrongly, it has always had a sort of consumer goods focused orientation, generally involving use of POS data to "pull" the rest of the supply chain.
But I think even many consumer goods companies aren't quite sure what demand-driven really means or what it takes to get there - and becoming demand-driven certainly applies to many more than companies in just that sector.
Let 2015 be the year you a least start the process of mapping out what a demand-driven supply chain really means to your industry and your specific company. I don't think many companies have actually documented that end state vision. That effort may just crystallize a road map of where your supply chain should be headed over the next 3-5 years.
Start Lunch Time Education Meetings: I know a few companies - Campbell Soup used to be one of them and maybe still is - that hold weekly or monthly Friday "brown bag" lunch days focused on education. Could be an internal team member presenting insight into their area of operation. Maybe someone from finance comes in and explains cash flow. Some have commented to me that sometimes watch SCDigest videos of interest and then talk about what they saw.
Whatever it is, I think this is a great idea for team building and knowledge gaining. People in supply chain are so busy these days they often just can't keep up with developments outside their immediate work responsibilities. A well-led brown bag Fridays program can really pay off at no real cost - think about launching one in 2015.
I am out of space, but think those are a pretty good list of supply chain resolutions for 2015. Pick a few off and run with it.
Any reaction to Gilmore recommended supply chain resolutions for 2015? What would you add? Let us know your thoughts at the Feedback button or section below.
|