![]() |
|
![]() |
 |
![]() |
 |
|
 |
 |
|
By Dan Gilmore - Editor-in-Chief |
|
|
|
|
|
|
|
Feb. 15, 2013 |
|
|
|
|
|
|
|
There are as always many things to do in the supply chain, but I am going to suggests that most companies add two priorities that are in the "important but perhaps not urgent" category, as the late Stephen Covey used to say. Those are both mapping and modeling your supply chain.
There is actually some close connection between those two initiatives efforts, but some separation as well.
Gilmore Says: |
As Toyota executive vice president Shinichi Sasaki said at the time, "Our assumption that we had a total grip on our supply chain proved to be an illusion."
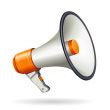
Click Here to See
Reader Feedback |
I believe mapping and modeling the supply chain will answer two fundamental questions that nevertheless many companies cannot well answer today: (1) What does my expended supply chain really look like? and (2) How does it really work, in terms on inputs and outputs?
So I am going to start with the mapping part today, and we'll finish with the modeling imperative next week. My original intention was to do both in one column, but I found there just isn't room.
So consider this: In the Spring time frame of last year, Toyota announced a number of steps designed to help it mitigate the type of supply chain disaster it experienced after the Japanese earthquake and tsunami in 2011. That disruption cost it hundreds of millions of dollars and for a while its place as the largest automotive manufacture in the world.
That impact came in large part not so much from damage to Toyota's own facilities, but rather from the huge challenges the company had getting parts or assemblies from tier one suppliers. In turn, that was often because those tier 1s could not get parts or materials from tier 2 or tier 3 suppliers, many of which Toyota did not even know were cogs in its supply chain.
So here we have supply chain icon Toyota being in effect blind to a significant portion of its own supply chain. As Toyota executive vice president Shinichi Sasaki said at the time, "Our assumption that we had a total grip on our supply chain proved to be an illusion."
Sometime in 2011, Toyota undertook what must have been a massive effort to map its full supply chain, and when the news about the project came out last March news, the company said the effort could only be 60% or so completed, because some tier 1 suppliers would not disclose their own vendors for competitive reasons.
Why am I pretty confident that this effort was massive? Because last year on one of our videocasts, Dr. Tom Choi of Arizona State University described his project to fully map the Honda Accord supply chain for just one sub-system - the center console. Based on a grant from the National Sciences Foundation, the effort took him three years, and provided Honda with visibility it simply didn't have for just that one system, let alone an entire automobile (see graphic below - actual supplier names have been genericized).
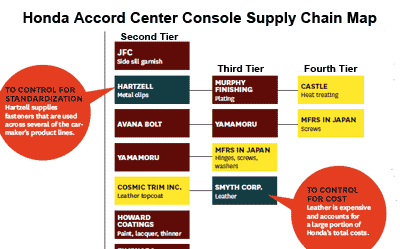
See Full Size Image
You most likely have also seen the news about the fire at the apparel factory in Bangladesh in late 2012 that killed more than 100 workers in a plant that was a walking fire trap with no exit doors in many areas of the building.
That already big news turned into a bigger story when it was discovered the facility was making products for store shelves at Walmart, Sears and other big name retailers, most of which said they did not even know the factory was one of their suppliers.
How did this happen?
Walmart gave one supplier a large contract for garments that was beyond the capacity of that supplier on its own, so it sub-contracted some of the work to others, including the fatal factory.
Jahangir Alam, an officer for ethical sourcing at Walmart's office in Dhaka until late 2011, said at the time that "with multiple sub-contracts going on, it has become almost impossible for buyers to practice ethical sourcing in the true sense." In others words, they really did not know Walmart's true supply chain.
Just in the past few weeks, Walmart has now issued tough new guidelines that bar suppliers from sub-contracting work to any facility it doesn't know about. But as big as Walmart is, it's just one company.
And of course, if you have been following the bizarre story of horse meat (and maybe even donkey meat) entering the retail and restaurant supply chain in parts of Europe for what was supposed to be all beef, you will know it was again the work ( it appears) primarily of a rogue supplier working for the main vendor. (See our Supply Chain Video News with CSCMP on Monday morning for more details on this on-going scandal.)
And while we are on this topic, sales at Yum Brands' hugely successful KFC stores in China plummeted 41% in January, after excessive levels of antibiotics, which accelerate growth, were found in its chicken. The stock price has tanked.
So the question again is: do you really know your full supply chain?
Within a few weeks of each other early last year, Toyota and my friend David Simchi-Levi of MIT started talking about the concept of time-to-recovery, or TTR. Toyota stated then it had set a goal of reducing its supply chain TTR at each facility from six months to just two weeks. And as Simchi-Levi has brought into relief with his innovative "Risk Exposure Index," TTR of course drives the total financial impact (FI) from a supply chain disruption, and together TTR and FI enabling companies both to assess what risk mitigation strategies might be worth and the value of lowering TTR.
But Toyota obviously can't reach its goal if it doesn't have clear visibility to its full supply chain. If a specific single source tier 2 supplier goes down for three months, it is possible that the tier 1 supplier downstream is then also down for three months as well? What parts are in fact single sourced by suppliers? Does that source have multiple production facilities? Are there other sources for the part in the larger marketplace? Are all the suppliers for this product or category in the same geographic area, meaning a single natural disaster could wipe out all the supply (as happened in some categories from the Japanese earthquake and then later with the Thailand flooding).
(By the way, the Toyota suppliers that would not disclose some or all of their own suppliers are making commitments to work with Toyota to achieve the same two-week TTR goals).
Or, switching industries, can you fully trust that a tier 1 food supplier isn't using slaughterhouses that are mixing in some horse meat or farms that are using too much antibiotics?
On the same videocast reference above, Tom Linton, now Chief Procurement & Supply Chain Officer at Flextronics, noted other problems with "outsourcing your bill of materials" to tier 1 suppliers.
For example, when he was previously at LG Electronics, Linton said there was naturally much angst and uncertainty in early 2009 after the financial crisis as to whether the electronics industry would recover relatively quickly, or stay in the dumps as it had been for several months. The market direction chosen would have big impacts on manufacturing capacity planning, inventory levels, etc.
Having previously taken the step of mapping its supply chain, Linton visited some of the tier 2 or 3 semiconductor foundries with which it did not do business directly - and he saw that electronics business was strong and recovering, if not yet clear at the end of the chain. This enabled Flextronics to get a several months jump on some competitors in preparing for the rising demand that did in fact occur, a jump worth tens of millions of dollars to the company in the end.
There is no doubt that mapping your full supply chain is a big effort, and the bigger a company is likely the more massive that effort is.
I used to think Apple's supply chain had become a bit over-rated, just meaning it seemed as Apple's product portfolio and innovation took off, then suddenly people were talking about Apple's supply chain prowess when in fact it was rarely called out for supply chain before the iPod and iPhone.
But I am changing my mind on this, in part because Apple clearly has not "outsourced its bill of materials," and maintains clear visibility and control of its extended, multi-tier supply chain without owning any of it.
So: to map your supply chain is to know your supply chain. And interestingly enough, mapping your supply chain (at least in part) is generally also where you start in a supply chain modeling effort. And that is where we will continue next week, including some really smart comments from our own expert Dr. Michael Watson of Northwestern University.
Do you agree it is time more companies map their full supply chains? Have you done so? Let us know your thoughts at the Feedback button (email) or section (web form) below.
|
|
|
|
 |
|
 |
![]() |
|
|
Recent Feedback |
Mapping the supply chain is difficult only in that it takes effort and commitment. The commitment must come from the participants in the chain, the links, both externally and internally. While you reported the challenges of looking up the supply chain through the layers of suppliers, it may not be as much of a “protecting proprietary information” than a matter of saving face, not wanting to admit that they don’t know.
Looking down the chain through the layers of manufacturers, distributors and retailers can be just as difficult. The food manufacturers face this issue with product recalls. Why? Because nobody set out designing their process first – it just evolved into the process that it is.
Business processes are more evolutionary in design than most managers want to or are willing to admit. Consider the old story of how the road network in New England evolved. The story goes that the network is the product of bovine engineering, where the cows on the way home from the central square decided their paths, and stuck to them. How many business processes are the product of the people that actually did the tasks? And how many processes are the product of the way the ERP system was programmed? By design?
Many companies find that they are inadequately mapped for their internal processes. The mapping challenge goes beyond just the flow of material. Companies, large and small, do not have a comprehensive map of the current flows of information, decision, or money, let alone the flow of the products. Industrial engineers working the floor operations of manufacturing plants and distribution centers map out the physical flows to eliminate waste, but the back office processes are rife with waste. While there are examples of well mapped processes in large companies, these are rare examples. You will be hard pressed to find a $500 million - $1 billion revenue per year company that has a comprehensive map of the internal flows. Here is another thought, you will be just as hard pressed to find many companies with over $1 billion with defined maps of the flow of money, material and information.
Mapping the process is a fundamental first step to figuring where the waste and delay hides. But not many companies value the process, they see it as a waste, mainly through a misconception of what the mapping process should do, what the outcome should be. So many don’t know how to do the process quickly. And that "so many" include the consultants that claim that they know what they are doing.
David Schneider
President
David K. Schneider & Associates
Feb, 15 2013
|
Mapping the entire supply chain or value chain should be undertaken not only for understanding where possible risks are, but also for training employees and benchmarking your processes. Total visibility is not known to many folks in the supply chain which can be a learning and mentoring opportunity to grow talent and expertise. In addition, the full supply or value chain starts with suppliers’ suppliers but continues to customer’s customer.
At ADTRAN we mapped the entire value chain and posted the supply chain mapping models around a large conference room. We broke it down into 14 major functions with best in class KPI’s displayed alongside our current KPI’s to understand where we stood in the industry and where we needed to improve. An eye opener to many, but a “must have” to build on current success and eventually develop a BI Business Intelligent dashboard for analysis and quick response, or as you state, understanding TTR –Time To Recovery.
In addition we employed the old adage “Trust but Verify”. Our Transportation Director, with the mapped model in hand, then visited and tracked the flow of raw materials and finished goods from supplier to customer opening up additional opportunities to reduce time, waste and costs.
Modeling the full supply chain opens up a cornucopia of opportunities that keeps on benefiting the company, the employees and the customers.
Tom Dadmun
VP ADTRAN Retired
ADTRAN
Feb, 15 2013
|
About time someone said this - I have worked with many companies over the last 15 years and am amazed at how many of them only have parts of their supply chains mapped. There is so much to be learned by mapping the entire supply chain.
I was working on a collaborative planning project a few years ago. We mapped the entire process and when we presented this to the two companies they vigorously disputed the process map. After doing the mapping themselves they quickly realized that over the years they had both lost visibility of how the processes had evolved. Now both companies have mapped all their supply chain, finding many other "blind-spots" that they were unaware of.
Mark Barratt
Associate Professor in Supply Chain Management
Marquette University
Feb, 15 2013
|
Excellent article.
We at Lehigh University and our Supply Chain Risk Consortium are violently in agreement with you on both threads.
We teach Supply Chain Risk Management at the graduate level and are supporting this emerging discipline of supply chain excellence with global workshops, education through APICS’ new SCRM CERTIFICATE of Achievement and an upcoming book for the classroom and more.
Through four years of teaching and global workshops, it seems 95% of all manufacturers do NOT map their supply chains!
We are advocating SC mapping be one of the First exercises one champions, if one plans to develop a solid SCRM journey to Identify, Assess, Mitigate and Manage risk.
We are also advocating new SCRM metrics such as T-t-R, Time-to-Recovery, VaR-Value at Risk and Resiliency Indexes.
In our new 21st Century Supply Chain Maturity Model, Predictability is the next stage in this risk journey, after Visibility. This means “Stress Testing” one’s supply chain with “What-if” scenarios using Probabilistic Models, NOT deterministic methods.
Dan, looking forward to the next installment on Modeling.
Very exciting times in the world of global supply chains and risk management.
Greg Schlegel
Executive in Residence, Center for Value Chain and Research Adjunct Professor, Supply Chain Risk Management
Lehigh University
Feb, 15 2013
|
I would suggest a precursor to the mapping, and that is to adopt analytics throughout the supply chain. The use of analytics will identify the elements of your supply chain mapping project that should be prioritized because of their impact to the rest of the line and therefore the organization as a whole. Supply chain analytics will also quickly identify root cause for trouble spots (e.g., PPV too high, OTIF too low, etc.) and thereby enable corrective action for first order effects - such as your buyer not paying standard cost for components. Mapping the supply chain will identify second and third order potential effects. Finally, supply chain analytics are now supported by Big Data databases that also read in unstructured data - such as the impact of that fire in Bangladesh. With appropriate analytics in place, supply chain management could have reacted ahead of the curve and made adjustments in sourcing to minimize its impact. There's really no reason why leading companies shouldn't be adopting analytics in their supply chain - without them, how can they know how well the line is functioning and where to focus their improvement efforts?
Gary Meyers
CEO
FusionOps
Feb, 20 2013
|
Thanks for underscoring the importance of mapping supply chains.
In my supply chain courses it is the first learning activity for the delegates after the introduction. The charts produced then go on the wall and stay there for the rest of the course.
David MacLeod
Principal
Learn Logistics Limited
Feb, 21 2013
|
Great article. Here are four advices from our practical experience:
1. Supply chain mapping is a living system that graphically represents your supplier network.
It does not mean building a model of your supply chain only once. Data changes all the time.
To handle this living system you need a database in the backend. Every stakeholder should have access to this database so all users have the same understanding of the supply chain.
Maps can either be geographical or an abstract network design. This maps have to be generated automatically out of the data.
2. Our understanding is, that supply chain mapping is not about business process - it is about relations between companies.
The database holds master data of suppliers (and sub-suppliers) and information about the relationships between these companies.
When you think about the supply chain, you immediately think of a deliverable relationship. But in reality, the chain includes financial relationships, partnerships, etc.
You have to handle a complex system.
3. Do a top down apporach (regarding your products)
By including product structures, such as bill of material, the downstream supply chain is readily visible when a product is displayed.
Using exact bills of material, the system will become too complex. Therefore use product groups in the first place. You can go into details later.
4. Start with the information that is already available within your company.
Usually a lot of information (even about second and third tier suppliers) is available within your company.
Identify all stakeholders within your company. Define processes to collect data. Think about supplier audits.
Start entering (importing) this data into the database.
In a second step you can ask your suppliers and sub-suppliers to enter data directly into your supply chain mapping database.
For more information go to www.supply-chain-mapping.com
Stefan Zeeb
General Manager
th data GmbH
Feb, 24 2013
|
Great article. Here are four advices from our practical experience:
1. Supply chain mapping is a living system that graphically represents your supplier network.
It does not mean building a model of your supply chain only once. Data changes all the time.
To handle this living system you need a database in the backend. Every stakeholder should have access to this database so all users have the same understanding of the supply chain. Maps can either be geographical or have an abstract network design. This maps have to be generated automatically out of the data.
2. Our understanding is, that supply chain mapping is not about the business process - it is about relations between companies. A database holds a master data of suppliers (and sub-suppliers) and information about the relationships between these companies. When you think about the supply chain, you immediately think of a deliverable relationship. But in reality, the chain includes financial relationships, partnerships, etc.
You have to handle a complex system.
3. Do a top down approach (regarding your products). By including product structures, such as bills of material, the downstream supply chain is readily visible when a product is displayed. Using exact bills of material, the system will become too complex. Therefore use product groups in the first place. You can go into details later.
4. Start with the information that is already available within your company. Usually a lot of information (even about second and third tier suppliers) is available within your company. Identify all stakeholders within your company. Define processes to collect data. Think about supplier audits. Start entering (importing) this data into the database.
In a second step you can ask your suppliers and sub-suppliers to enter data directly into your supply chain mapping database.
Stefan Zeeb
General Manager
th data GmbH
Mar, 20 2013
|
I am taking on a project to map the supply chain at one of our sites. I was wondering if anyone has a set of best in class KPIs for the supply chain that I could adopt for my value stream map.
Pat Dugan
Master Black Belt
Bristol Meyers Squibb
Mar, 18 2016
|
Great article - thank you for sharing. I am a research analyst/PhD candidate at ITLS (institue for transport and logistics studies) at Sydney University in Australia, My reserach is based on using network theory to model supply chains. Therefore supply chain maps are an important aspect for my studies. Would you be kind enough to let me know where I can find a real world supply network map (hopefully a large data set)? Your response would be greatly appreciated.
Supun Perera
Research Analyst
Institute of Transport and Logistics Studies
Jun, 24 2016
|
Our company also sources ingredients and materials from our vendors. We are also relying on tier 2/3 suppliers that we do not know about. Just like the example above (Toyota) we rely heavily on these suppliers and don't even know who they are. Mapping out a supply chain might prove to be difficult as some of our vendors will not tell us who their supplier is because of its competitive advantage.
Steven Tung
Operations Manager
Tab Labs Inc.
Sep, 24 2019
|
I strongly belive that companies need to map their full supply chain, no matter how small or big they are. The bigger they are, the more neccessary to do so, though. I doubt such an extensive job has been already done by our Supply Chain Manager.
MARYAM JABERI
Sr Strategic Sourcing Manager
SGS
Jan, 27 2021
|
Yes, I agree. It has always been important to understand the map of your supply chain. We have done so too by incorporating the subcontracting clause in our contracts. This has given us strong understanding with respect to, reliability and scrutiny of tier 1 and tier 2 suppliers.
Rishabh Sharma
Vendor Manager
TD Bank
May, 24 2021
|
|
|
|
|
![]() |
 |
![]() |
 |
|
|
|
![]() |
|
|