Demand for distribution space near major US ports continues to be strong, such that available real estate in many markets is almost gone. That situation in turn is pushing rates for existing space higher and higher.
So along comes distribution real estate and management company Prologis with an idea new to the US but common in Asia and Europe: build multi-level, multi-purpose distribution facilities close to the ports to reduce real estate costs.
Supply Chain Digest Says... |
|
|
In fact, Prologis just recently broke ground on such a new facility near Seattle, the first of its kind in the US, according to a report in the Journal of Commerce. The 590,000 square-foot facility will have three levels, and be located two miles from the Port of Seattle and five miles from Seattle's downtown.
Of course, multi-level warehouses were once common in US cities, but handling inefficiencies at these buildings and the move of millions of people from cities to the suburbs, where land for DCs was relatively inexpensive, soon made multi-level DCs obsolete.
But maybe they are coming back in style.
DC vacancy rates around major US ports is very low currently, often less than 3%. What's more, land suitable and available for building DCs in the popular 500,000 to 1 million square foot footprint is hard if not impossible to find in these markets. In the Seattle market where Prologis is building its new facility, the DC vacancy rate in Q4 was just 1.8%, according to the quarterly analysis from real estate form Jones Lang Lasalle.
Land prices have also soared for any land that is available, sometime to the point of making an investment for distribution not financially viable, forcing importers to either look to other ports or to secure sites farther and farther from port complexes, adding time and costs. JLL says land values near Seattle have shot up 20% to 25% over just the last two years.
Prologis is said to the facility will be targeted at several different logistics services for the three-story structure. Those include import distribution, regional distribution and ecommerce fulfillment all from the one building, which was built "on spec" hoping the clients will come.
The first two stories (see image below) will focus on crossdocking and transloading and have truck ramp access, using a sort of mezzanine approach on the second level. The third story will focus on storage and replenishment services, and will be served by freight elevators. Back to the future, it seems.
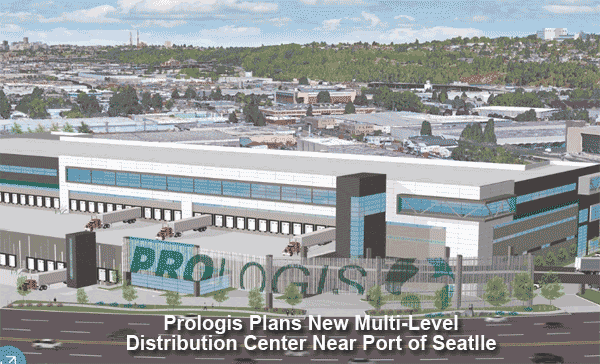
"Major urban areas are running out of industrial space," said Hamid Moghadam, chief executive of Prologis last November. "The only way the logistics sector can compete is with this more dense format."
(See More Below)
|
CATEGORY SPONSOR: SOFTEON |
|
|
|
|
But such services won't come on the cheap. The JOC quotes John DeCesares, president of consulting firm WCL Consulting, as saying rates in these kinds of close-to-port facilities will be as much as three times what it might cost for 3PL services say in the Kent area of Washington state, much further away from the port. DeCesares said that the location will enable better time to market in this ecommerce era, trumping the higher logistics costs for some companies.
And that equation may only work for the highest volume importers that can transload or crossdock all of their goods.
"If you put it on the floor close to the port, that won't work," Fred Jorhring, president of drayage firm Golden State Express, told the Journal of Commerce.
While it has to see if this first effort will pan out, Prologis says it sees similar opportunities near the ports of Oakland, Los Angeles/Long Beach, and New York/New Jersey.
The JOC story notes there are many existing facilities near ports - often former manufacturing sites - but that commonly they are just 100,000 to 200,000 square feet. Building up, as Prologis is doing, may be a way to rejuvenate that land, similar in a sense to the multi-story DCs being built by Amazon and others now in urban areas to support efulfillment.
The concept of these "infill" facilities that have multiple levels will be familiar to some US companies operating logistics operations across the globe, as they are common in parts of Asia and Europe where land around ports has been an issue for some time. Singapore and parts of Japan are especially known for using this approach.
The new Prologis facility is scheduled to open sometime in 2018.
What do you think of this DC plan for Prologis? Will is work? Let us know your thoughts at the Feedback section below.
Your Comments/Feedback
|
Bruce H. Anderson
Consultant, Pauder Design |
Posted on: Apr, 20 2017 |
|
If there is no room in the city (often the case) AND no room relatively close, then this might make sense. However, if typical DCs are relatively close, like in the Seattle/Kent market (actually a little south of Kent) this may not fly. Delivery speed is nice, but there may be a point where speed gets far too expensive to justify, much like airfreight which is a shadow of its former self. |
|
|