|
 |
|
 |
|
|
Achieve New Levels of Performance in Warehousing and Distribution with our Outstanding Logistics Training Program |
|
|
|
|
 |
The Very Best
Workshop on Improving Distribution
Center /
Warehouse Management Available
Today |
 |
|
In
a world of offshoring, increasingly
demanding customer requirements, high-velocity order fulfillment and continuous
logistics challenges, distribution
excellence has never been more important
to both supply chain and corporate
success.
In
this outstanding two-day workshop,
part of Supply Chain Digest’s
Professional Education Series, you’ll
gain the knowledge, insight and tools
you need to take your company’s
distribution performance to world
class levels. With a proven curriculum,
led by one of the logistics
industry’s more knowledgeable
and experienced practitioners - Ken
Miesemer, former Director of Distribution
and International Logististics at
Hershey Foods. Ken Miesemer is supported by SCDigest Editor Dan Gilmore, who will present on supply chain execution software systems.
Best Practices
in Distribution Center Design, Operations
and Management will improve your
own capabilities and your company’s
supply chain effectiveness.
It's
not just theory - you’ll leave
our workshop with practical action
plans that can be implemented
right away.
The Fall Schedule is complete - look for the Spring Schedule Soon!
To ensure you receive information, email us at info@scdigest.com |
|
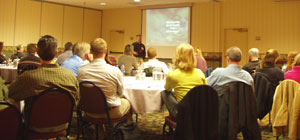
Here’s what attendees said about our Spring Series Workshop:
“One of the best seminars I have ever attended. Very practical – not just theory. Helped me enormously.”
Logistics Manager – SC Johnson
“The class was extremely detailed and helpful. Learned some excellent concepts to be utilized at my company and DC. Great seminar!”
DC Manager, Lifetime Fitness
Workshop
seats are truly limited in order to make the
experience personal and interactive.
When we hit our capacity, we can no
longer accept additional registrations,
so reserve your place today.
How
You Will Benefit from the Best
Practices in Distribution Center
Design, Operations
and Management Workshop
This
course isn’t just outstanding
education. It’s a dynamic, interactive
experience that will challenge your
thinking, and enable you to interact
with your professional peers.
The
course and materials include a number
of tools and templates for use in
distribution analysis and decision-making
that are worth the cost of the course
by themselves – and which you
can put to work right away in your
operations.
By
the end of this two-day training course,
you will be able to:

|
Deploy
best practices for improving labor
productivity, operations efficiency,
and inventory accuracy
|

|
Apply proven
techniques to improve distribution
center strategy and execution
|

|
Master the
technology tools available
to distribution managers
|
|
Discover how
to achieve the operational
flexibility needed for today’s
ever-changing supply chain
|
|
Enhance the efficiency
of your inbound and outbound
logistics |
|
Develop distribution
performance and financial measurement
systems that drive continuous
improvement and alignment with
broader supply chain and corporate
goals |
|
Implement advanced
techniques for inventory and
distribution management
|
|
Make greatly
improved outsourcing decisions
– and achieve better results
from 3PL partnerships |
|
Course
Outline |
Day 1
Module
1 - Case Study – Starting-Up
a World Class DC (A Fortune 500 Company)

|
Rebuilding an
entire distribution network
|

|
Network and
inventory optimization
|

|
Effective
Project Management
|
|
Building and
material handling equipment design
|
|
Selecting
a Third Party Logistics Provider
(3PL)
|
|
Selecting
and Implementing a Warehouse Management
System (WMS)
|
|
Employee training
and labor management
|
|
Metrics for
warehouse performance –
financial, productivity, and quality
|
Module
2 - Optimizing DC Facility Layout
and Operations

|
The principles
of efficient storage and handling
systems design
|

|
Factors
to consider when selecting design
and storage systems |

|
Throughput
vs. storage capacity |
|
Dock
designs to match the business
profile |
|
Configuring
the storage systems |
|
Testing
the design through automation
|
|
How
to maximize storage density |
Module
3 - Planning For Efficient Materials
Flow
Module
4 - Inventory Management and Control

|
Inbound
Advanced Shipment Notifications
(ASN’s) and Bar Code/RFID
receiving
|

|
Cycle
counting vs. physical inventories
|

|
Where
the Count-back process excels
|
|
Controlling
internal losses |
|
Load
Integrity Programs |
|
Tools
to control overs, shorts, and
damages |
|
Distribution
alliance - a partnership that
wins |
Day
1 Review and Discussion
|
|
Day 2
Module
5- DC Performance Measurement - Planning
For Efficient Use of Labor And Equipment
Resources

|
Metrics
- tracking and managing all warehouse
activities
|

|
Measuring
and comparing KPI’s –
internal, supplier and customer
KPI’s |

|
Labor
Management Systems - workforce
performance management |
|
Engineered
standards development and implementation |
|
Fostering
a culture of continuous development
and improvement |
|
Workforce
incentive plans |
Module
6 - Selecting and implementing Enabling
Technologies (WMS, LMS, Slotting,
RF, Voice, etc.)

|
Overview
of available technology options
|

|
What
the vendors won’t tell you
about how to select the solution
that’s right for you |

|
The
selection team and process |
|
Requirements
definition |
|
Building,
then trimming, the candidate list |
|
How
do you really differentiate the
solutions?
|
|
Implementation,
project management and best practices |
 |
Ongoing
refinement and enhancement |
Module
7 - Selecting and partnering with
a 3rd Party Logistics Provider (3PL)

|
Viewing
the 3PL as a partner not a supplier
|

|
Selection
is more than a Request For Proposal
(RFP) - how to build knowledge
before making your decision |

|
Bid
specifications redefined - what
is really important?
|
|
The
three phases from start-up to
steady state |
|
Setting
performance standards |
|
Rate-based
vs. cost plus commercial agreements
|
|
Process
manuals - defining the expectations
|
Module
8 - Cost Plus And Gain Sharing –
An Alternative To Rate-Based Agreements

|
Why
cost-plus vs. rate-based agreements?
|

|
The
concept of risk drives 3PL margin
expectations - how do we control
this? |

|
Budgeting,
actual costs, and the variance
explanation process |
|
Fixed
management fee, base fee, and
incentive fee structures |
|
Implementing
activity-based costing and cost-plus |
|
Using
a cost-plus type process in your
own operations
|
|
Gain
sharing - the correct incentive
for 3PL performance |
Supplementary
Course Materials Review
Day
2 Review and Discussion
|
Additional
Information
Registration
Fees
Current Course
Schedule/On-Line Registration
Course
Brochure
Instructors
Program Providers |
Registration
Fees

|
$2995.00
per person |
|
Registration
fee includes: two-day
course, workshop binder with slides
and templates, continental breakfast
and lunch each day, free parking.
|
|
The
lead instructor, Ken Miesemer, will
also provide post-workshop support
by answering questions from attendees
on specific distribution problems.
|
|
Discounts for multiple registrants from one company - contact us for details |
The
preferred method of registration is
to use our secure, on-line process
(powered by Verisign), which requires
payment by any major credit card (see
class schedule below).
You
will first be taken to the registration
page for your chosen session/venue,
and then to the Verisign/Payflow site
to complete the transaction (including
receipt).
If
you want to register on-line, but require other payment methods
(such as paying by check or an invoice),
register in the same way, but follow
the directions on the registration
confirmation page for other fee arrangements,
or email us at info@scdigest.com.
To download a Registration Form and submit by mail or fax, go here: Downloadable Form
|
Schedule
and On-Line Registration
Spring Schedule will be announced soon!
|
|
City |
Location |
Dates |
Event ID |
Register |
|
|
|
|
|
|
|
|
|
|
|
|
|
|
|
|
|
|
|
|
|
a
|
|
|
|
|
|
|
Hotel Information
|
|
About
Your Instructors
Lead Instructor Ken
Miesemer, CPIM CIRM, is currently a
Sr. Consultant at the St. Onge Company
with a focus on Supply Chain improvement
projects.
Ken
has worked with many multinational
clients and benchmarking partners
to solve distribution issues.
He
had previously been with The Hershey
Company for 15 years with the most
recent title of Director, Distribution
and International Logistics, overseeing
approximately 4 million square feet
of distribution center operations
in the mainland U.S., Hawaii, Puerto
Rico, Mexico, Canada, and Hershey
International Operations.
Ken’s
career provided experiences in Materials
Management, Systems Implementations
(MRP/ERP, Supply Chain Planning and
Execution Systems), Program Management,
Distribution Operations, and International
Logistics. He had the opportunity
to define, consolidate and then manage
several national distribution networks.
At Hershey Foods, Ken had been involved
with several large projects including
the start up of the new 1.2 million
square foot Eastern Distribution Center
III and the standardization of processes
across the national network. Hershey
opened a new 1.1 million square foot
Distribution Center in the St. Louis
area in 2004.
Ken
is an active speaker at the Warehouse
Education and Research Council (WERC),
CSCMP, and APICS, and authored the
book, Start-Up of a World Class
DC. He currently serves on the
Board of Directors as President of
WERC, an association of distribution
professionals.
|
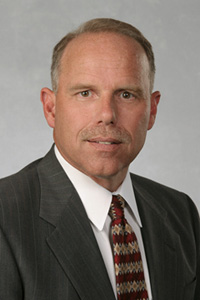
Ken
Miesemer
Best
Practices in Distribution Center
Design, Operations
and Management Workshop
Leader |
|
Dan Gilmore, Editor of Supply Chain Digest, is a world class expert on supply chain execution systems. He will lead a section of the Workshop on SCE software. |
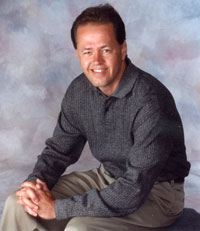
Dan Gilmore
Editor
Supply Chain Digest
|
|
Distribution
Best Practices Workshop Program Providers
|
|
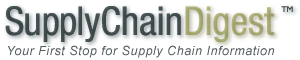
Supply
Chain Digest™ is the industry’s
premier interactive knowledge source, providing
timely, relevant, in-context information.
Reaching tens of thousands of supply chain
and logistics decision-makers each week,
our flagship publications - Supply Chain
Digest and SCDigest On-Target - and website
deliver news, opinions, information, education,
and training to help end users improve supply
chain processes and find technology solutions.
www.scdigest.com |
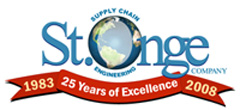
St.
Onge Company was founded in 1983 as
an independent consulting engineering company.
Over the past 20 years, we have grown into
a global company with over 75 consultants,
engineers and project managers. We are headquartered
in the rolling foothills of York, Pennsylvania,
midway between Baltimore and Harrisburg.
In
recent years, we have developed offices
in Europe, China, and the Middle East to
better serve our international clients wherever
they may need our assistance around the
world.
www.stonge.com
|
|
|
|
|
 |
|
 |
|
|
|
|