The analysts at IDC Manufacturing Insights have just released a report based on a major survey of supply chain executives and managers, among the highlights of which is that companies see the highest opportunity for supply chain cost reduction from better procurement effectiveness and deployment of Lean/Six Sigma methodologies more deeply into their operations.
SCDigest Says: |
Ellis and Knickle had the same reaction we did to this data, commenting that "What seems a bit odd is the fact that manufacturers still see responsiveness through the lens of increase demand forecast accuracy.
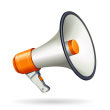
Click Here to See Reader Feedback
|
The study surveyed more than 300 supply chain professionals in manufacturing companies across a wide range of titles and types of firms, both in terms of size and industry sector.
The type of manufacturer was almost even split four ways along the segmentation scheme IDC adopted a few years ago, placing manufacturers as being asset-oriented (e.g., chemicals), brand-oriented (e.g., consumer goods companies), engineering-oriented (automotive, aerospace), or technology-oriented (e.g., high tech).
About 48% of respondents identified themselves as "product-focused' companies, versus roughly 36% saying they were cost-focused, and another 16% saying they were service-focused.
Report authors Simon Ellis and Kimberly Knickle suggest there are four key trends most impacting the manufacturing supply chain environment right now:
(1) The "empowered consumer" who has access to considerable information and alternatives, and is increasingly demanding very rapid fulfillment.
(2) Complex and extended global supply networks that are a consequence of globalization and the chase for "low cost" manufacturing - but the expected results often are not being realized.
(3) Increasingly volatile demand that has become the "new norm," driven by many factors that together "conspire to drive forecast accuracy down and demand volatility up, requiring greater supply chain agility if service performance is to not suffer.
(4) Growing regulation, particularly in the area of traceability.
(5) Increasingly volatile and generally rising direct input costs, especially as many manufacturers lack the ability to make price increases stick. (See Will Companies Retain Ownership of Products they Sell to Harvest and Re-Use the Materials they Contain?)
Although more companies identified themselves as product-centric rather than cost or service-centric, reducing overall costs was the top rated supply chain priority. Ellis and Knickle suggest that there is still some discrepancy between 'what we say we do' and 'what we do,' though we would argue this may be simply that the supply chain views product innovation as mostly engineering and marketing's job. (We'll save the debate over the supply chains role in innovation for another time.)
After reducing costs came "responding more quickly to supply and demand changes," followed by "improve product quality/safety."
So, what tools and techniques to supply chain managers see as most fruitful to reduce overall supply chain costs?
Perhaps somewhat surprisingly, "reducing procurement costs" dominated the results, with some 35% of respondents citing it as the top opportunity, versus just 18% or so for the number 2 response, which was "establish or expand Lean/Six Sigma" type improvement methodologies. Just behind was reducing transportation and logistics costs, as shown in the figure below.
Top Tactics to Reduce Supply Chain Costs
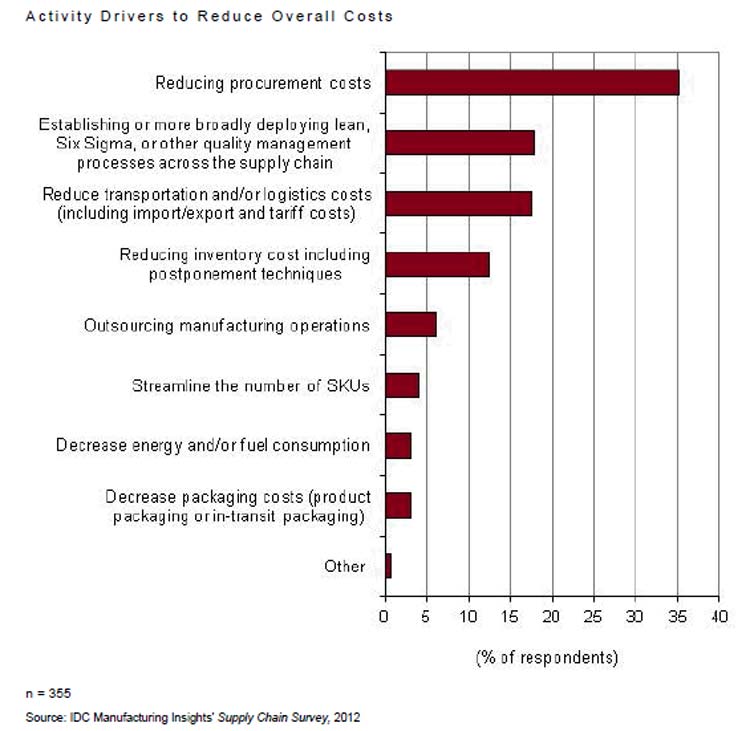
Does that ranking reflect a simple reflex to look at purchasing to find a way to beat suppliers up for lower prices?
Not really, IDC says, given the increasing concern about inflation and input costs, and the reality that purchased materials are generally the largest single source of cost for manufacturing supply chains.
(Supply Chain Trends and Issues Article - Continued Below)
|