SCDigest Editorial Staff
|
SCDigest Says: |
|
Bartholdi and Hackman make the interesting observation that very large docks should probably not be I-shaped, or at least only designed that way with caution.
Click Here to See Reader Feedback
|
The interest in cross docking continues to be high, even if the actual implementation of cross docking outside of the retail sector is still modest at best.
The opportunity to reduce distribution and sometimes inventory costs through cross docking is a powerful incentive for more companies to consider the practice - though there are many challenges, especially for non-retailers that must be more specific in how goods are fulfilled for customer shipments and cannot take advantage of the "door per store" concept often used in retail.
Whirlpool is one manufacturer that has found success employing a cross dock concept, broadly using the strategy to move appliances through its newly re-designed distribution network, where cross docking became a key element in its roll-out of much fewer, larger DCs across the country that were able to meet two-day delivery windows across the US.
Which leads to an interesting question - is there a clear type of building shape that lends itself to optimal cross docking?
The answer as usual in supply chain and logistics matters is "It depends."
There are a number of factors that might go into cross dock building design.
The most important one may be whether the building is meant to be primarily or even exclusively a cross dock operation, versus planned cross docks in combination with traditional wave picking or other fulfillment models. Clearly if significant storage and pick, pack, ship operations are required, there are much different layout requirements than that for a pure cross dock facility.
The land available for the building may also come into play, perhaps eliminating some design considerations.
That is especially true given that the number of doors planned for the facility (current and future) is an essential design consideration. Because unloading and inspection, if used, generally require less time than loading, most cross dock facilities plan for more outbound than inbound doors, though the timing of the inbound receipts and outbound loading can impact how this is factored, as well plans for labor (i.e., putting more labor on outbound, working extra shifts, etc.).
Whether there are plans for full, partial or little material handling automation will also impact the design, often actually requiring more floor space, but at the gain of increased throughput and productivity. Whether automation makes sense operationally and economically also depends heavily on the units to be handled - potentially a smart move for cross docking cartons or totes (common in retail), but less so for full pallets or other types of handling units. Mix is important.
Dr. John Bartholdi and Dr. Steven Hackman of Georgia Tech note that there are trade-offs in terms of cross dock DC size, number of doors, and efficiency.
"Cross docks with many doors are generally less efficient than cross docks with fewer doors," they note in a supplement to their book Warehouse & Distribution Science. "The reasons are as follows. A door can only have a few near neighbors on a dock and so a dock with more doors means that each door is likely to have few more near neighbors but many more distant neighbors. This means that in general freight must move farther across a large dock. Consequently, labor costs are generally higher at larger docks." (Note from Dr. Bartholdi:"The chapter on crossdocks is based on work done with Kevin Gue of Auburn University. Indeed, both Steve and I consider Kevin "The" expert in academia on crossdocking.")
Another factor in cross dock DC design is how rapidly the inbound shipments will flow to outbound trailers. In some cases, that can be almost as soon as an inbound load is received, but in other scenarios - especially outside of retail - some inbound goods must be stored or staged for hours or even days, and that swell time must be accounted for in the design.
I-Shaped is Most Popular Design
In the same supplement, Bartholdi and Hackman note that an I-Shaped design is the most popular for cross dock buildings.
"Most cross docks are long and skinny rectangles, shaped like the letter I," they note. "The reason for this is so that freight can be unloaded from an arriving trailer and carried the short distance across the dock to be loaded into an outbound trailer (across the dock)."
That in fact is the shape Home Depot chose for its new distribution network of cross dock-based regional distribution centers (RDCs) that the company has been rolling out across the country. The footprint below, outlined in orange within the larger total real estate footprint (parking, etc.) is for an approximate 650,00 square foot new cross dock RDC in Monroe, OH that opened in 2010.
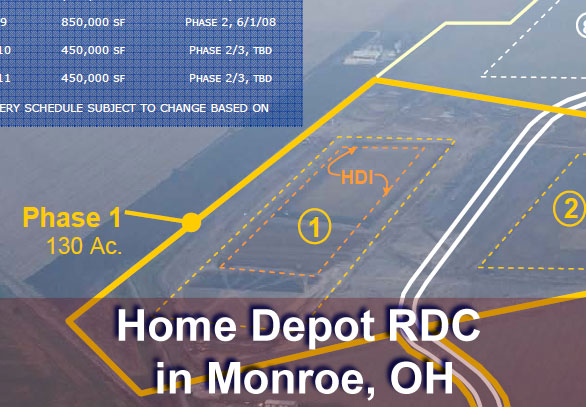
(Distribution Article - Continued Below)
|